Technologia obróbki powierzchniowej w CNC: zwiększenie wartości dodanej produktu
Rola obróbki powierzchni w technologii CNC
Technologia obróbki powierzchni odgrywa kluczową rolę w zwiększeniu trwałości i estetycznego wykończenia produktów wyprodukowanych metodą CNC. Stosując techniki takie jak anodowanie i nanoszenie piankowego pokrycia, producenci mogą znacząco przedłużyć żywotność elementów. Te procedury zmniejszają częstotliwość wymiany i napraw przez zwiększenie odporności powierzchni na zużycie i korozyję. Na przykład, powierzchnie anodowane są znane z zdolności wytrzymywania surowych warunków środowiskowych, co zostało potwierdzone badaniami wskazującymi na poprawę wydajności w warunkach korozyjnych.
Ponadto, poprawa trwałości za pomocą obróbki powierzchniowej znacząco zwiększa również estetyczny wygląd produktów. Techniki takie jak piaskowanie czy polerowanie zapewniają elegancki, precyzyjny wykończenie, które podkreśla atrakcyjność wizualną. Jest to szczególnie ważne w konkurencyjnych rynkach, takich jak motoryzacja i produkty konsumpcyjne, gdzie wygląd produktu może przyciągnąć uwagę klientów, zwiększyć ich zadowolenie i wzmacniać lojalność wobec marki. Dobrze wykonany produkt nie tylko wyróżnia się, ale również przekazuje jakość i niezawodność, co jest kluczowe dla budowania długoterminowych relacji z klientami.
Obróbka powierzchniowa dotyczy więc nie tylko ochrony, ale również stanowi narzędzia do różnicowania produktów na rynku.
Popularne techniki obróbki powierzchniowej w CNC
Techniki obróbki powierzchni są kluczowe w zwiększaniu trwałości, funkcjonalności i estetycznego atrakcyjnego wyglądu części wykonywanych metodą CNC. Dzięki zrozumieniu korzyści i zastosowań tych technik, przedsiębiorstwa mogą lepiej chronić swoje produkty, przedłużać ich żywotność oraz przyciągać klientów.
Anodowanie dla części z aluminium
Anodowanie to ważna metoda obróbki powierzchniowej, która jest przede wszystkim stosowana dla części z aluminium, znana z zwiększania odporności na korozyję i twardości powierzchni. W tym procesie elektrolitycznym tworzy się warstwa utleniny, która chroni aluminium i umożliwia jego barwienie w celach estetycznych. Statystyki wskazują, że anodowane aluminium może trwać do pięciu razy dłużej niż nierozpracowane aluminium w środowiskach outdoorowych. Ta długowieczność jest nieoceniona w branżach takich jak lotnictwo i motoryzacja, gdzie trwałość ma kluczowe znaczenie. Ponadto, anodowanie zwiększa opór na tarcie i izolację elektryczną, co czyni tę technikę niezastąpioną w aplikacjach wysokowydajnych. Ta metoda obróbki powierzchniowej aluminium nie tylko przedłuża cykl życia części, ale również pomaga w poprawie ich wyglądu wizualnego.
Naprawa powłok pudelkowych do zwiększenia ochrony
Naprawa elektroforetyczna oferuje odporną warstwę ochronną przed korozyjami i uszkodzeniami mechanicznymi, stosując suchy proszek i nagrzewając go, aby utworzyć trwałe wykończenie. Ta metoda nie tylko oferuje wiele rodzajów kolorów i wykończeń, co zwiększa atrakcyjność produktu, ale jest również bardziej zrównoważona w porównaniu do tradycyjnych farb ciekłych. Najnowsze raporty branżowe podkreślają, że powierzchnie obsadzane proszkowo prezentują się lepszą jakością i trwałością. Ponadto, malowanie proszkowe emituje zaniedbywalne ilości związków organicznych lotnych (VOC) podczas aplikacji, co jest zgodne ze ścisłymi regulacjami środowiskowymi. Kombinacja wysokiej jakości wykończeń i ekologicznego podejścia czyni malowanie proszkowe doskonałym wyborem dla przemysłu szukającego zarówno ochrony, jak i wzmacniania estetyki, jednocześnie minimalizując wpływ na środowisko.
Przetarcie kulkami do matowego wykończenia
Obróbka piaskowana jest popularną metodą przygotowania powierzchni, wykorzystującą szkliste kule abrazji do stworzenia jednolitego matowego wykończenia na częściach metalowych. Ta technika odgrywa kluczową rolę w poprawie przylegania farb i pokryć, co zwiększa jakość i trwałość ostatecznego produktu. Piaskowanie kulami jest szczególnie cenione w zastosowaniach przemysłowych, gdzie precyzyjna tekstura przyczynia się do funkcjonalności. Oprócz zalet technicznych oferuje atrakcyjne matowe wykończenie, które spełnia różne wymagania rynku, od produktów konsumenckich po wysokiej klasy komponenty przemysłowe. Dzieki swoim zaletom estetycznym i funkcyjnym, piaskowanie kulami stanowi uniwersalny narzędzie w technikach przygotowania powierzchni.
Maszyna do czyszczenia stali nierdzewnej Usługa obróbki blachy
Niestandardowe usługi OEM/ODM
Dostosowane usługi Original Equipment Manufacturer (OEM) i Original Design Manufacturer (ODM) są kluczowe w przemyśle maszyn do czyszczenia z nierdzewnej stali. Te usługi pozwalają producentom dostosowywać rozwiązania do konkretnych potrzeb klientów, zapewniając bezproblemową integrację z istniejącymi systemami i komponentami. Ta personalizacja jest szczególnie cenna w takich przemysłach jak medyczny i samochodowy, gdzie dokładna zgodność i standardy wydajności są niezbędne. Badania pokazują, że firmy korzystające z dostosowanych rozwiązań tendencją do doświadczenia większego zadowolenia klientów, ponieważ te usługi są sprawnie projektowane do radzenia sobie z unikalnymi wyzwaniami operacyjnymi.
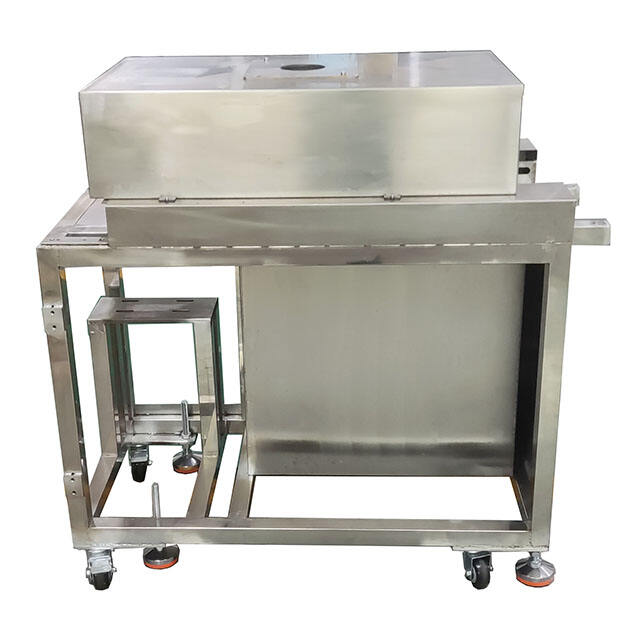
Materiały i opcje obróbki powierzchniowej
Wybór materiałów i opcji obróbki powierzchni jest kluczowym krokiem w produkcji z nierdzewnej stali. Różne gatunki nierdzewnej stali oferują różne właściwości, takie jak różny poziom odporności na korozyję i wytrzymałość, co czyni je idealnymi dla konkretnych zastosowań. Obróbka powierzchni, takie jak pasywacja, polerowanie i nanoszenie pokryć, dalszym etapem wzmacnia te właściwości. Dane branżowe sugerują, że odpowiedni wybór metod obróbki powierzchni może przedłużyć żywotność materiału o do 50%, podkreślając wagę tych decyzji zarówno dla efektywności, jak i długowieczności w różnych zastosowaniach.
Przewagi precyzyjnego obrabiania CNC
Precyzyjne obróbka CNC oferuje wiele zalet, w tym wysoką dokładność, powtarzalność oraz możliwość tworzenia złożonych geometrii. Te korzyści znacząco poprawiają wydajność produktów, zwłaszcza w kluczowych sektorach, takich jak lotnictwo i medycyna, gdzie precyzja jest krytyczna. Zgodnie z analistami branży, precyzyjna obróbka CNC może zmniejszyć marnotrawstwo materiału o do 30%, promując w ten sposób zrównoważone praktyki produkcyjne i poprawiając kosztową efektywność. Korzystając z zaawansowanej technologii CNC, producenci mogą spełniać surowe standardy jakości i wydajności, jednocześnie minimalizując wpływ na środowisko.
Wybór odpowiedniego rodzaju obróbki powierzchniowej dla Twoich części wykonywanych metodą CNC
Czynniki do uwzględnienia: materiał i zastosowanie
Podczas wybierania rodzaju obróbki powierzchniowej dla części wykonywanych metodą CNC, ważne jest uwzględnienie specyfiki materiału ze względu na ich różnorodne reakcje na te obróbki. Na przykład, aluminium często poddawane jest anodowaniu w celu zwiększenia odporności na korozyję i twardości powierzchniowej, podczas gdy stal może korzystać z galwanizacji dla dodatkowej ochrony. Ponadto, unikalne wymagania aplikacji, takie jak narażenie na surowe chemikalia lub potrzeba określonego wyglądu, odgrywają kluczową rolę w decydowaniu o najlepszym rodzaju obróbki. Raporty sugerują, że dostosowane obróbki powierzchniowe mogą znacząco poprawić wydajność części mechanicznych w trudnych warunkach, co potwierdza ich wagę zarówno w zakresie długowieczności materiału, jak i jego funkcjonalności.
Koszt vs Trwałość: Wybór odpowiedniego rozwiązania
Zrównoważenie kosztu i trwałości jest kluczowe przy wybieraniu metody obróbki powierzchni dla części CNC. Choć tańsze opcje mogą wydawać się pociągające w krótkiej perspektywie czasowej, często prowadzą do wyższych kosztów długoterminowych z powodu częstego konserwowania lub wcześniejszych uszkodzeń. Analizy statystyczne wskazują, że inwestycja w bardziej odporne metody obróbki może obniżyć koszty cyklu życia o ponad 20%, co podkreśla ich wartość w praktykach zrównoważonego produkcji. To podkreśla potrzebę, aby producenci oceniali nie tylko bezpośredni koszt, ale również potencjalne oszczędności i zyski na efektywności wynikające z wyboru bardziej trwały metod obróbki powierzchni dla elementów CNC.
Wpływ obróbki powierzchni na dodatkową wartość produktu
Zwiększanie konkurencyjności na rynku
Efektywne metody obróbki powierzchni mogą istotnie zwiększyć wartość produktu poprzez poprawę jego estetyki, trwałości i funkcjonalności. Te ulepszenia czynią produkty bardziej atrakcyjnymi dla klientów i umożliwiają ustalanie wyższych cen, co z kolei wzmacnia konkurencyjność na rynku. Właśnie dzięki tym poprawkom produkty poddane obróbce wyróżniają się na rynku w stosunku do produktów nieobrobionych. Analiza rynku potwierdza tę tezę, pokazując, że firmy inwestujące w zaawansowane metody obróbki powierzchni często zgłaszają wzrost sprzedaży o 15% lub więcej w porównaniu z tymi, które tego nie robią. Ten trend podkreśla wagę obróbki powierzchni nie tylko w poprawie jakości produktu, ale również w napędzaniu wzrostu biznesowego.
Spełnianie standardów branży i oczekiwań klientów
Oberwładne metody odgrywają kluczową rolę w zapewnieniu, że produkty spełniają różne normy branżowe dotyczące bezpieczeństwa, wydajności i wpływu na środowisko, co zwiększa ich atrakcyjność na rynku. Zgodność z tymi normami chroni producentów przed potencjalnymi ryzykami prawno-ekonomicznymi oraz wzmacnia ich reputację wśród klientów i konsumenów. Badania wskazują, że przestrzeganie surowych standardów branżowych często prowadzi do poprawy utrzymywania klienta oraz zadowolenia, co jest kluczowe dla długoterminowego sukcesu biznesowego. Poprzez spełnianie oczekiwań klientów za pośrednictwem zgodności metod obróbki powierzchni, firmy mogą budować zaufanie i lojalność, co gwarantuje pozostanie konkurencyjnymi w dynamicznie zmieniającym się krajobrazie rynkowym.
Recommended Products
Hot News
-
zalety obróbki CNC
2024-01-16
-
Co to jest technologia obróbki CNC?
2024-01-16
-
trend rozwoju obróbki CNC
2024-01-16