CNC-koripuhallus: pyörivien osien valmistuksen toteuttaminen
Ymmärrys CNC-tornivalmistuksesta pyöriville osille
CNC (Computer Numerical Control) tornivalmistus on erikoistunut valmistustekniikka, jossa pyörivää työaineetta muokataan kiinteällä leikkaustyökalulla. Tämä menetelmä mahdollistaa tarkkojen ja toistettavien komponenttien tuotannon, erityisesti niiden osien kohdalla, jotka vaativat symmetrisiä suunnitteita pyörivän akselinsa suhteen. CNC-tornikoneet käyttävät tietokoneohjelmistoja automatisoidakseen valmistusprosessin, tarjoamalla epävertaisen tarkkuuden monimutkaisissa geometrioissa ja rautauspinnissa. Nämä koneet pystyvät käsittelemään erilaisia materiaaleja, tarjoamalla joustavuutta ja tarkkuutta erilaisten profiilien osien valmistuksessa.
CNC-tornauslaitekkeen erityispiirteistä yksi on sen korkea automatisointitaso. Tämä ei ainoastaan vähennä ihmisten osallistumista, vaan se parantaa myös merkittävästi tuotantotehokkuutta. Modernissa valmistustuoksiossa CNC-tornauslaiteke on arvokas resurssi, koska se mahdollistaa keskeytymättömän toiminnan usein vuorokauden ympäri, mikä optimoi läpiviemisen ja vähentää työvoimakustannuksia. Kyky tuottaa jatkuvasti osia tarkkoja määritelmiä noudattaen tekee CNC-tornauslaitteen erityisen hyödylliseksi sarjatuotannossa. Tämä kyky on ratkaiseva auto-, ilmailu- ja lääkinnällisen laitteistoilman teollisuudessa, joissa tarkkuus ja luotettavuus ovat ehdottomia.
Tärkeimmät menetelmät CNC-tornauslaitteessa
Tarkka tornaustechniikka
Tarkka pyöritys CNC-maalausprosessissa sisältää tiettyjen tekniikkien käyttämisen tiukempien toleranssien ja parempien pinta-terminien saavuttamiseksi. Tähän kuuluu pyörähdysnopeuden säätäminen ja kuljettuvauhtien optimointi, jotka ovat ratkaisevia lopputuloksen tarkkuuden ja laadun varmistamiseksi. Ilmailu- ja autoteollisuus vaativat näitä tarkkoja tekniikoita erityisesti komponenttinsa kriittisen luonteen vuoksi. Lisäksi edistyneiden CNC-ohjelmistojen ja erikoistyökalujen käyttö mahdollistaa yksityiskohtaiset suunnitelmat ja tarkat mitattavat arvot, mikä parantaa pyörityksen tarkkuutta ja tehokkuutta. Teknologian integrointi parantaa ei vain tuotantolaatua, vaan myös vähentää materiaalihenkilöä varmistamalla, että jokainen leikkaus tehdään äärimmäisen tarkasti.
Työkalupolkujen optimointi tehokkuuden lisäämiseksi
Työkalupolkujen optimointi on keskeinen menetelmä CNC-koripuhdistuskoneiden valmistuksessa, joka keskittyy valmistustehokkuuden parantamiseen. Työaikojen lyhentämisen ja jätteen vähentämisen avulla tämä prosessi alentaa merkittävästi tuotantomenoja ja lisää tuotannon läpimenoa. Ohjelmistomenetelmät näyttävät ratkaisevan roolin tehokkaimman leikkaustyökalun polun määrittelyssä, mikä on olennaista potentiaalisten törmäysten ja virheiden välttämiseksi leikkausprosessin aikana. Tämä ei vain varmista turvallisuuden ja tarkkuuden, vaan se myös parantaa valmistuskaaren yleistä tehokkuutta. Työkalupolkujen optimointi on ehdottomasti välttämätön teollisuudenaloille, jotka pyrkivät maksimoimaan tuotantoaan samalla kun minimoidaan kustannuksia, mikä on erityisen tärkeää kilpailukykyisissä aloissa, kuten autoteollisuudessa ja ilmailuteollisuudessa.
Edistyneet CNC-koripuhdistuskoneiden leikkausprosessit
Moni-akselinen CNC-käännös
Moniakselinen CNC-kierrätys vallankumauttaa monimutkaisia geometrioita tuottavien prosessien, sillä se mahdollistaa leikkausvälineen liikkuvan useilla aksereillä. Tämä kyky antaa valmistajille mahdollisuuden tuottaa yksityiskohtaisia osia suuremmalla tarkkuudella ja tarkkuudella, mikä on olennaista korkeateknologisissa aloissa, kuten lääketieteellisessä ja tarkkuusmitalluksessa. Moniakselisen CNC:n hyödyntämällä yritykset voivat laatia komponentteja, jotka täyttävät nämä alat asettamat ankarammat vaatimukset, varmistamalla luotettavuuden ja suorituskyvyn. Tämä edistyksellinen valmistusprosessi yhdistää käsitteellisen suunnittelun ja konkreettisen tuotteen, osoittamalla sen keskeistä roolia modernissa valmistuksessa.
Korkean nopeuden valmistus pyöriville osille
Korkean nopeuden moottorioperaatiot näyttävät keskeiseltä rooliltaan pyörimisaikojen vähentämisessä, mikä mahdollistaa valmistajille tuottavuuden ja tehokkuuden parantamisen. Nopeamman pyörivän moottorin ja syöttönopeuksien käyttö optimoi pyörivien osien jäljittelemistä, mistä seuraa merkittäviä aikatappioita. Tuottavuuden lisäksi korkeanopeudelliset CNC-torni-tekniikat edistävät parempia pinta-aineistoja sekä työkalujen kulumisen vähenemistä, tarjoamalla etuja sekä suorituskyvyssä että kestossa. Kun valmistajat pyrkivät tehokkuuteen, korkeanopeusmoottorioperaatiot erottuvat tärkeänä lähestymistapana tuotantotavoitteiden saavuttamiseksi ja korkeatasoisten standardien ylläpitämiseksi kilpailukykyisellä tahdilla.
Tutustu CNC-moottorituotteisiin
Alumiinisiirrettävät osat
Nopea prototyypin laatiminen mukautetun CNC-mahdollistaa merkittäviä etuja yrityksille, jotka tarvitsevat alumiiniosia suunniteltuun tarpeisiinsa. Tämä prosessi nopeuttaa osien luontia, mahdollistaen yrityksille testata ja kehittää suunnitelmiaan ennen sarjatuotannon aloittamista. Nopean prototyypin iteraatiomaisuus tukee muutoksia toiminnallisuuden ja ulkonäön parantamiseksi, varmistamalla, että lopullinen tuote täyttää markkinoiden vaatimukset.
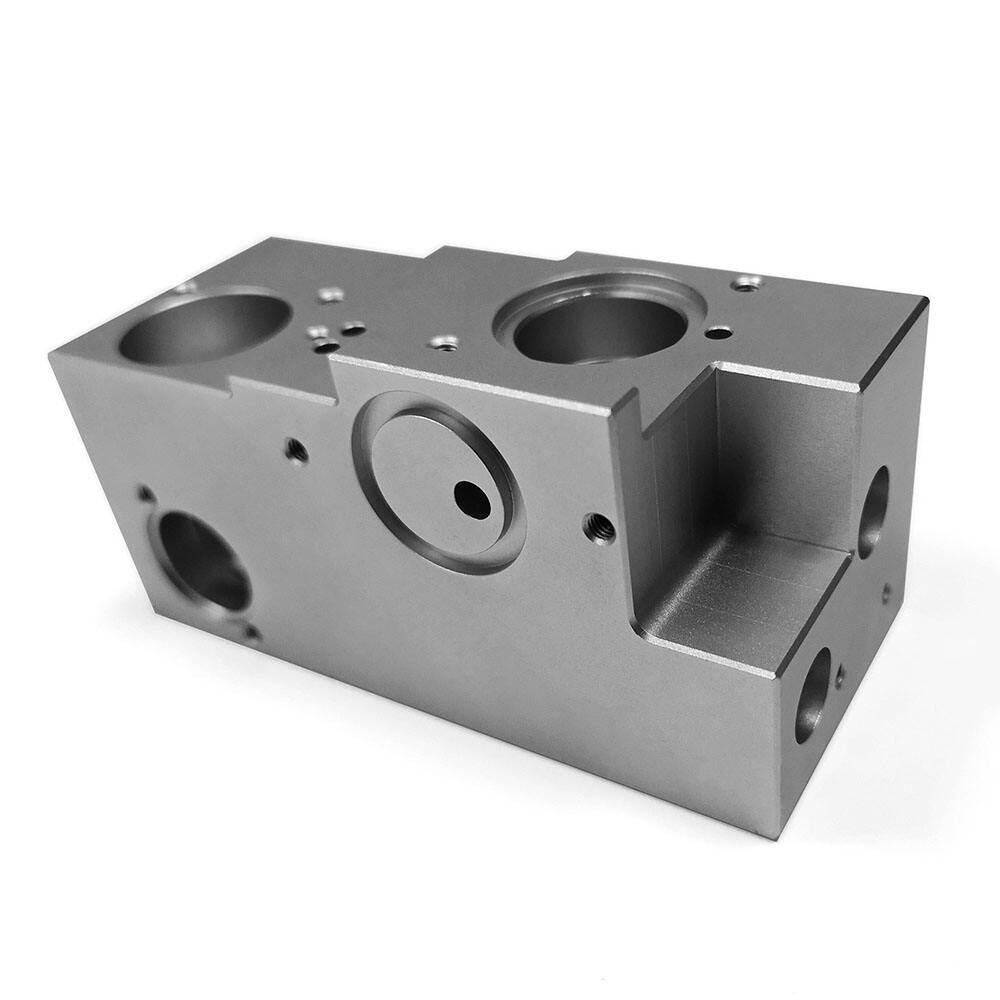
Väri Custom Sheet Metal Processing Laserleikkaus CNC Tarkkuosat
Laserleikkauksen teknologia on keskeinen osa CNC-montaussa, erityisesti teräsplaatin käsittelyssä, mahdollistaen monimutkaisien suunnitelmissa vaihtelevien värien ja pinta-terminoiden käytön. Tämä kehitys tarjoaa valmistajille laajemman valikoiman suunnittelumahdollisuuksia, mikä tekee komponenttien tuotannosta mukautettavaksi tiettyihin teollisuuden tarpeisiin. Kuluttajien elektroniikka- ja autoteollisuus hyötyvät suuresti tästä tarkkuudesta, joka varmistaa, että jokainen komponentti täyttää korkeat laadunormit.
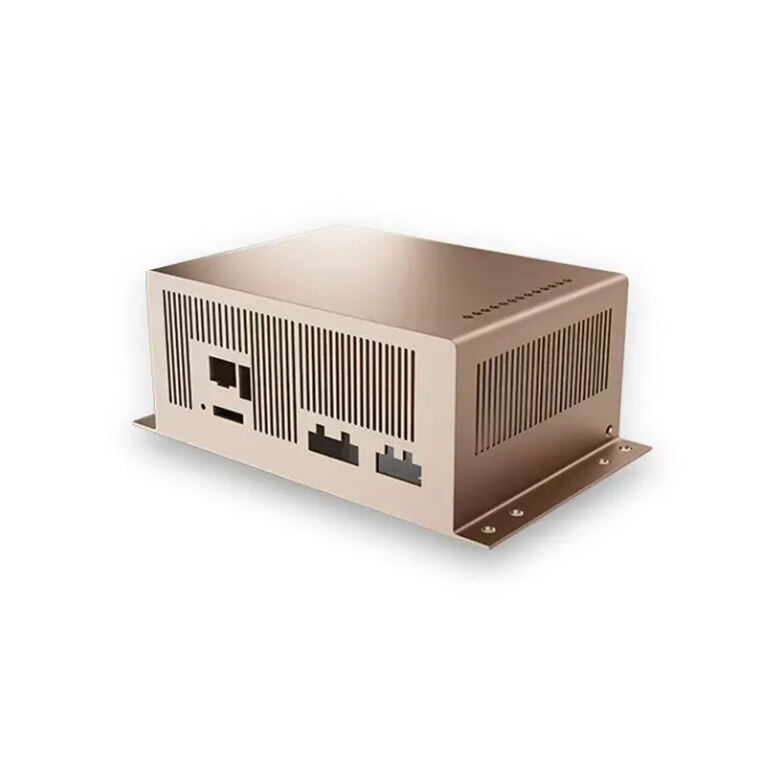
Mukautettu tarkkuus-CNC-myllynpalvelu metallilohkon käsittelyyn
Mukautetut tarkkuus-CNC-myllynpalvelut ovat keskeinen osa metallilohkojen jäsentelyssä täydellisiin mittatarkkuuksiin. Tämä prosessi sisältää tarkkoja säätöjä mittoihin ja pinta-terminoihin, vastaamaan erityisiin suunnittelusuorituksiin. Nämä palvelut tarjoamat tarkkuudet ovat olennaisia teollisuuden aloilla, kuten rakennustuotannossa ja koneen valmistuksessa, joissa tarkasti valmistetut metallikomponentit ovat ratkaisevan tärkeitä lopputuotteiden toiminnalle ja turvallisuudelle.
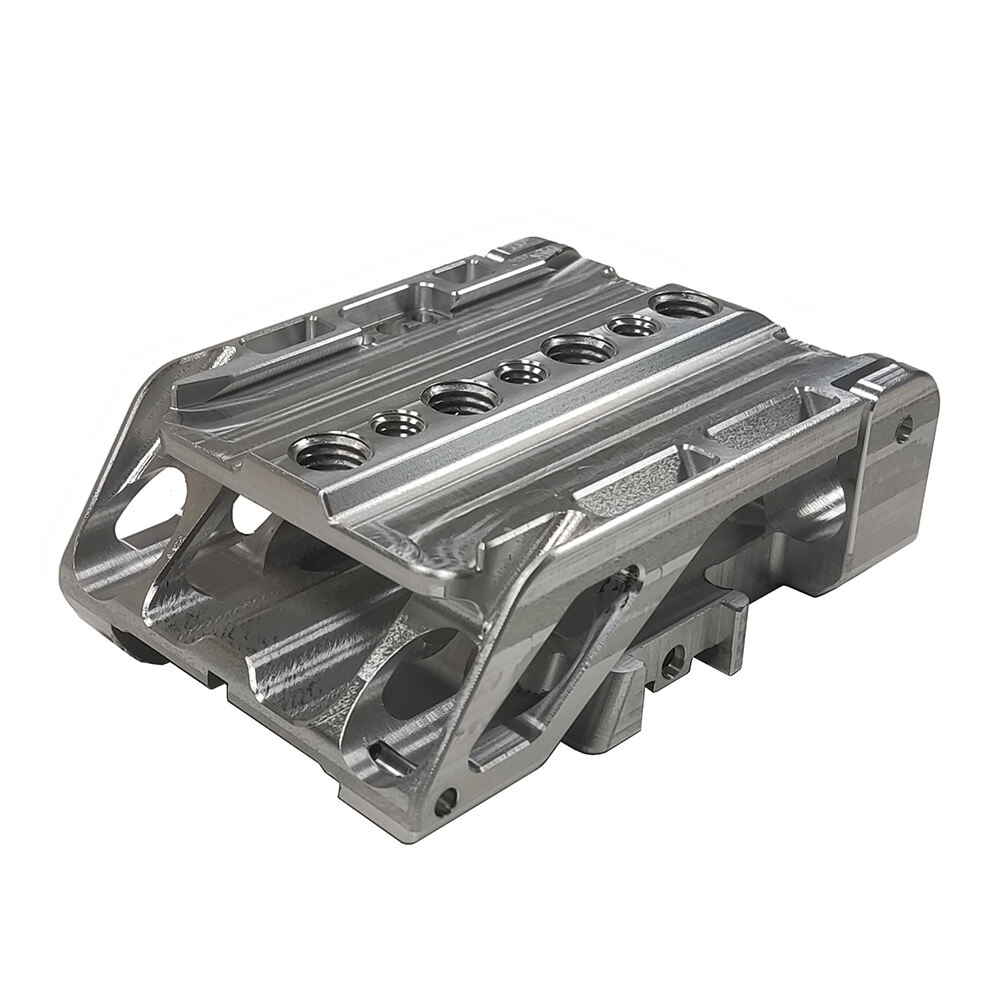
CNC-kylväysmekkojen sovellukset valmistuksessa
CNC-kylväysmekkojen käyttö ilmailu- ja avaruusteollisuudessa
CNC-koripuhdistus on ratkaisevaa lentoturvallisuuden ja suorituskyvyn standardien täyttämiseksi ilmailualalla. CNC-mekaanikkaa käytetään tarkkuudella, joka sallii toleransseja mikron sisällä, mikä on elintärkeää ilmailuosaisten monimutkaisille vaatimuksille. Tyyppisiä sovelluksia ovat turbiiniosien, kapeiden ja pyörivien osien valmistaminen, joissa valmistajat käyttävät edistyneitä materiaaleja, kuten titaninia ja kompositteja. Nämä materiaalit vaativat tarkkoja mittaustarkkuuksia kestääkseen lennon aikana kohtaamat korkeat paineet ja lämpötilat. Lopputuloksena on, että integroimalla uusimmat menetelmät CNC-koripuhdistus parantaa ilmailuosien luotettavuutta ja kestävyyttä, varmistaen niiden suorituskyvyn vastaavan alan ankaria määrityksiä.
CNC-koripuhdistus autotuotteissa
Autoteollisuudessa CNC-kaaritornikoneiden jalostus on keskeinen tekijä komponenttien valmistuksessa, jotka kestää vaativat olosuhteet samalla, kun varmistetaan optimaalinen suorituskyky. Prosessia käytetään laajalti monenlaisen tärkeiden osien, kuten vääntömoottoreiden, hampaiden ja moottoripohjien, tuotantoon. CNC-jalostuksen kyky edistää nopeaa kehitystä ja tuotantoa on ratkaiseva teollisuudessa, joka tunnetaan nopeasti etenevästä innovaatiosta ja kovasta kilpailusta. Nopean suunnittelujakson toistamisen ja monimutkaisia osia tehokkaasti tuottamisen avulla CNC-kaaritornikoneet tukevat autoteollisuuden tarvetta toimittaa korkealaatuista ajoneuvoja, jotka täyttävät jatkuvasti muuttuvat asiakkaiden odotukset ja sääntelyvaatimukset. Tämä jalostusprosessi ei vain tueta nykyisiä tuotannon tarpeita, vaan myös asettaa puitteet tuleville teknologisille kehittymissuunnille autoteollisuudessa.
Tulevaisuuden suuntauksia CNC-kaaritornikoneiden jalostuksessa
Automaatio CNC-kaaritornikoneiden jalostuksessa
Automaatio CNC-kaivopuhaltimen valmistuksessa vallankumouskaristaa tuotantoprosesseja parantamalla tehokkuutta, vähentämällä työvoimakustannuksia ja parantamalla tuotteen laadun johdonmukaisuutta. Robottien ja tekoälyn (AI) integroimisen avulla valmistajat voivat saavuttaa suuremman läpiveton, mikä tekee tuotantoriveistä joustavampia ja kykeneväisempää vastaamaan tiukkoja määräaikoja. Tämä teknologian integrointi muuttaa perinteiset kaivoprosessit täysin automatisoituiksi älytehtaiksi. Kun yritykset pyrkivät pysymään kilpailukykyisinä, automaation kehittäminen CNC-kaivopuhaltimen valmistuksessa ei ole vain trendi vaan tarve, joka antaa yrityksille mahdollisuuden hyödyntää teknologian edistystä parempien toimintatulosten saavuttamiseksi.
Kestävyys CNC-kaivopuhaltimen valmistuksessa
Kestävien käytäntöjen tavoitteena CNC-konepajakoneiden toiminnassa on vähentää huomattavasti jätettä, energiankulutusta ja hiilijalanjälkeä. Kun ympäristöongelmat kasvavat maailmanlaajuisesti, valmistajat ottavat käyttöön ympäristöystävällisempiä menetelmiä täyttääkseen säännölliset vaatimukset ja kuluttajien odotukset. Tärkeimmät tekniikat sisältävät työkalujen elinkaaren pidentämistä, materiaalien kierrättämistä ja prosessien optimoimista vähentääkseen energiaa. Nämä kestävät käytännöt vastaavat nykymarkkinoiden kasvavaa kysyntää vihreämmistä valmistusratkaisuista ja sovittelevat yritykset yhtiövastuun arvoihin. Siksi kestävien käytäntöjen hyväksyminen CNC-valmistuksessa muuttuu yhä enemmän teollisen sektorin perustavanlaatuiseksi käytännöksi.
Recommended Products
Hot News
-
CNC-koneiden edut
2024-01-16
-
Mikä on CNC-koneiden valmistusteknologia?
2024-01-16
-
CNC-koneiden kehityssuuntaus
2024-01-16