Mecanizado de chapa metálica: la tecnología CNC ayuda a una producción eficiente
El Papel de la Tecnología de Mecanizado CNC Eficiente en la Producción de Chapa Metálica
La tecnología de mecanizado CNC eficiente desempeña un papel crucial en el campo de la producción de chapa metálica, combinando la tecnología informática con la fabricación metálica para lograr niveles excepcionales de precisión. El mecanizado CNC integra el diseño asistido por computadora (CAD) con maquinaria controlada por computadora precisa, permitiendo cortar y dar forma a la chapa metálica según especificaciones exactas. Este nivel de precisión es vital en industrias como la aeroespacial y la automotriz, donde los componentes a menudo requieren tolerancias tan ajustadas como ±0,005 pulgadas. Esta precisión asegura que los componentes encajen perfectamente en ensamblajes complejos, mejorando tanto la calidad como la fiabilidad.
La adopción de la tecnología CNC en la producción de chapa metálica automatiza los procesos de mecanizado tradicionales, mejorando considerablemente la eficiencia. Con la implementación de sistemas CNC, las empresas han reportado aumentos de productividad de hasta un 30%. Este incremento se debe principalmente a tiempos de preparación reducidos y a errores manuales minimizados, lo que permite salidas más consistentes y confiables. Además, la automatización de los procesos reduce la dependencia del trabajo cualificado y disminuye el potencial de error humano, optimizando aún más las líneas de producción. Como resultado, el mecanizado CNC se está volviendo indispensable para lograr una fabricación de chapas metálicas económica y de alta calidad en la manufactura moderna.
Técnicas Clave para Optimizar el Mecanizado CNC en Chapa Metálica
Técnicas Avanzadas de Mecanizado CNC Multi-Eje
El mecanizado CNC multi-eje es fundamental para producir formas complejas y características detalladas en una sola configuración, reduciendo significativamente el tiempo operativo y mejorando la precisión de la producción. Esta capacidad es particularmente crucial para crear componentes intrincados que a menudo se requieren en maquinaria moderna. Por ejemplo, industrias como la aeroespacial y la fabricación de dispositivos médicos dependen del mecanizado multi-eje para geometrías precisas y complejas. Al minimizar las configuraciones, las máquinas multi-eje no solo optimizan el flujo de trabajo, sino que también disminuyen los puntos de error potenciales en el proceso de mecanizado.
El uso de software avanzado para la programación multi-eje optimiza las trayectorias de las herramientas y mejora la coordinación de las máquinas. Con la integración de técnicas de programación sofisticadas, los fabricantes han reportado una reducción en el tiempo de mecanizado de hasta un 20%. Esta optimización asegura que el proceso de mecanizado sea más eficiente, reduciendo movimientos innecesarios y mejorando la producción general. Tales eficiencias en la programación y ejecución benefician significativamente los ciclos de producción, lo que lleva a tiempos de entrega más rápidos y ahorros de costos.
Optimización de Trayectorias de Herramientas para una Producción Más Rápida
La optimización de trayectorias de herramientas es una estrategia vital en el mecanizado CNC para reducir movimientos innecesarios y aumentar la velocidad de producción. La implementación de estrategias de avance adaptativo puede llevar a una mayor eficiencia y mejores acabados superficiales. Este enfoque permite a los operadores ajustar las velocidades dinámicamente según el material y las condiciones de corte, optimizando cada operación de mecanizado para la velocidad sin comprometer la calidad.
El uso de herramientas de software específicas para simular y analizar trayectorias de herramientas puede mejorar aún más las estrategias de diseño. Estas herramientas permiten a los fabricantes visualizar y optimizar los movimientos de las herramientas antes de la producción real, lo que puede llevar a una reducción significativa del tiempo. Los estudios indican que dichos esfuerzos de optimización pueden resultar en una reducción del 15% en el tiempo de operación de mecanizado. Una efectiva simulación de trayectorias de herramientas no solo acelera los plazos de producción, sino que también mejora la precisión del producto final, reforzando la importancia de la planificación estratégica en el mecanizado CNC.
Beneficios del Mecanizado CNC para la Producción de Chapa Metálica
Aumento de la Velocidad de Producción con Enrutadoras CNC
Las fresadoras CNC están revolucionando la producción de chapa metálica al ofrecer operaciones de alta velocidad, aumentando significativamente las velocidades de producción. Permiten a los fabricantes manejar grandes volúmenes de manera eficiente, optimizando así los flujos de trabajo operativos. Los datos sugieren que la implementación de fresadoras CNC puede mejorar la velocidad de producción en más del 25% en comparación con los métodos tradicionales. Esta mejora se traduce en una mayor rentabilidad al minimizar los tiempos de entrega y maximizar la producción. Al integrar fresadoras CNC en sus procesos, los fabricantes pueden mejorar su ventaja competitiva en el panorama manufacturero en constante evolución.
Reducción de residuos mediante operaciones precisas de torno CNC
Las operaciones de torno CNC son fundamentales para minimizar el desperdicio de material, lo cual es particularmente vital en la producción de chapa metálica debido a los altos costos asociados. Estas máquinas permiten mediciones exactas y estrategias de corte planificadas, lo que conduce a una reducción significativa del desperdicio. La investigación indica que las empresas que adoptan sistemas de torno CNC informan una disminución del desperdicio de hasta un 30%, mejorando la sostenibilidad de sus operaciones de fabricación. Esta reducción no solo disminuye los costos de producción, sino que también apoya prácticas amigables con el medio ambiente, alineándose con las iniciativas modernas de sostenibilidad en el sector de la fabricación.
Explorando productos de maquinaria CNC para chapas metálicas
Mecanizado CNC de Precisión Personalizado OEM de Aleación de Aluminio fresado Piezas de Acero Inoxidable
El mecanizado CNC de precisión personalizado OEM es esencial para los fabricantes que necesitan altos estándares en el fresado de aleaciones de aluminio y piezas de acero inoxidable. Este proceso combina calidad con eficiencia, permitiendo soluciones a medida que cumplen con requisitos específicos de la industria. Con la adaptabilidad de las máquinas CNC, los fabricantes pueden manejar pedidos personalizados de manera eficiente, lo que resulta en ciclos de producción más rápidos. Los datos de la industria respaldan esto, indicando un 40% menos de tiempo de espera para pedidos personalizados gracias a las capacidades CNC, lo que mejora significativamente la productividad operativa.
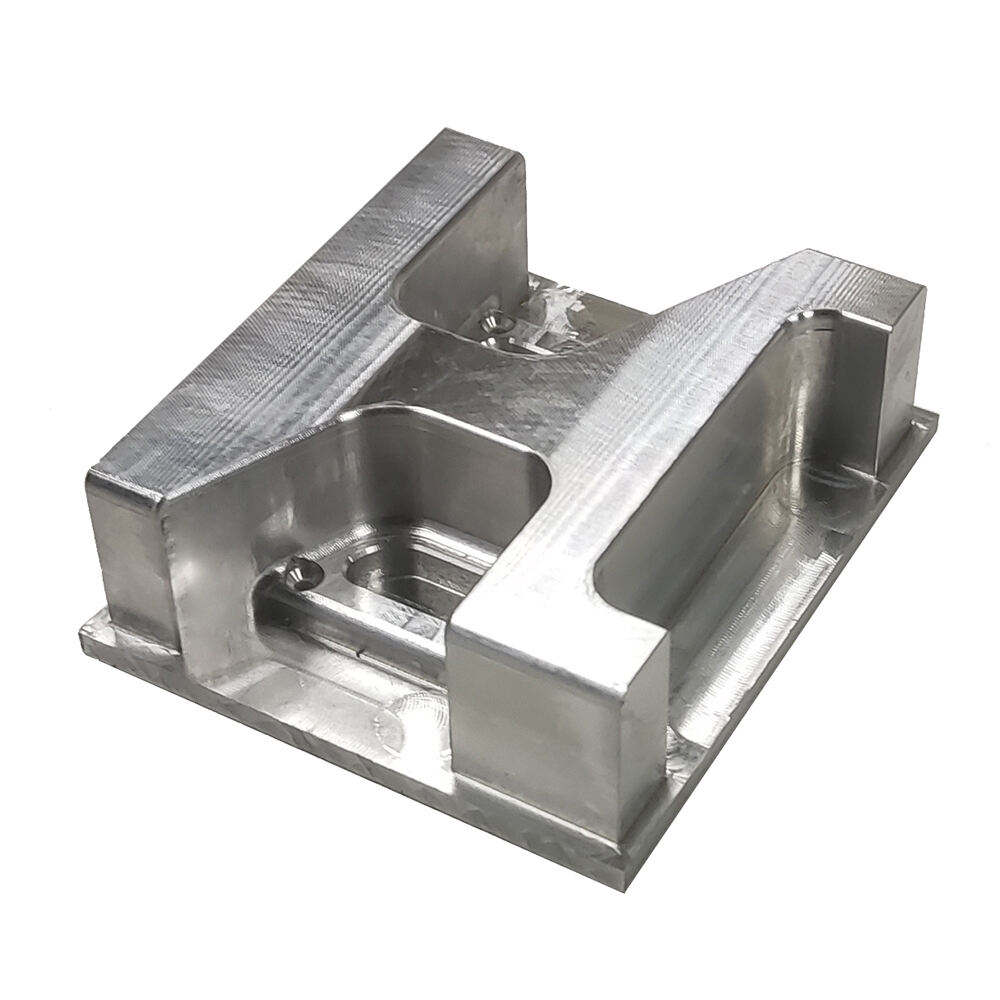
OEM precisión a medida mecanizado CNC de acero inoxidable fresado piezas de aluminio
El mecanizado CNC especializado para piezas de acero inoxidable y aluminio es crucial en industrias que requieren componentes duraderos y confiables, como la automotriz y la aeroespacial. Estos sectores se benefician enormemente de la alta precisión y consistencia ofrecidas por las máquinas CNC. Las empresas OEM aprovechan esta tecnología para producciones personalizadas de bajo volumen, lo que conduce a mejoras notables en eficiencia. Las estadísticas muestran un aumento del 35% en la eficiencia de producción utilizando CNC, en comparación con los métodos tradicionales, permitiendo la excelencia en aplicaciones de alta apuesta.
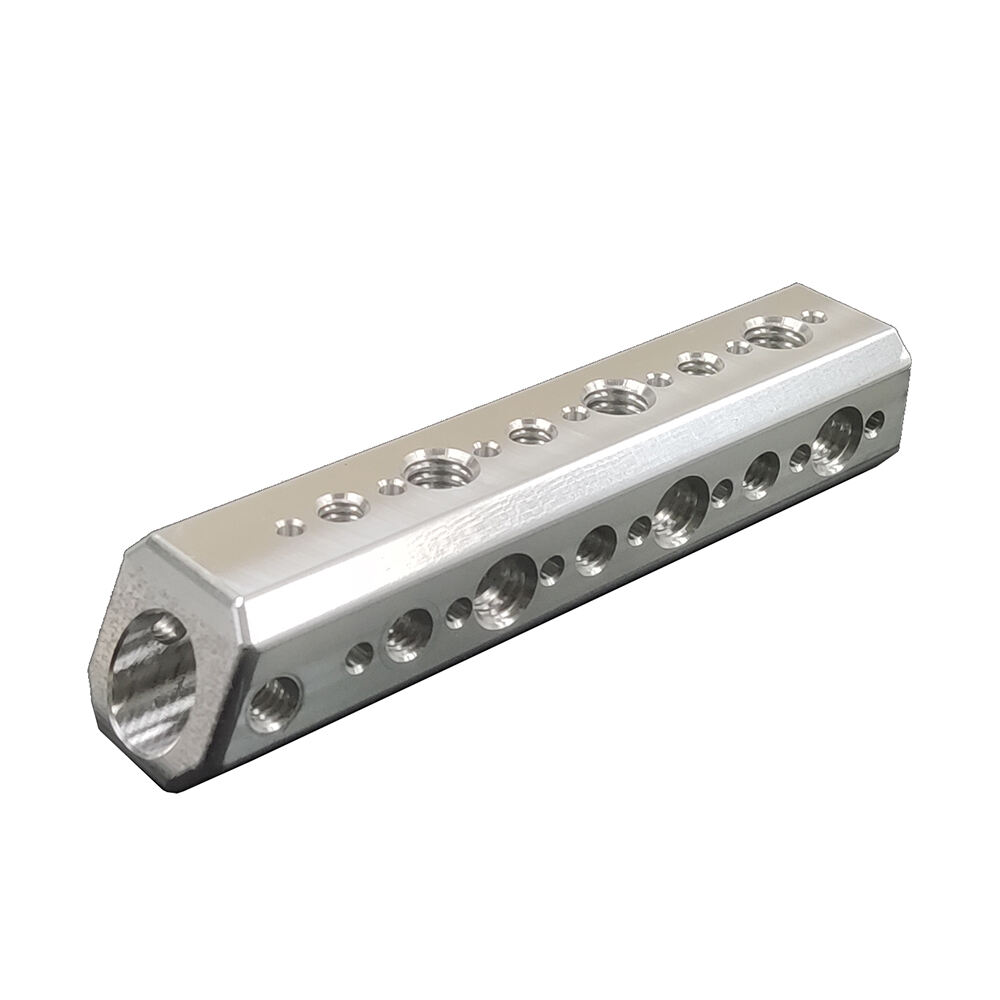
Corte Láser de Chapa Metálica Perforado Doblez Procesamiento Acero Inoxidable Soldadura CNC
El corte láser CNC es un cambio de juego para las aplicaciones de chapa metálica, proporcionando máxima precisión y velocidad. Esta tecnología permite la creación de diseños intrincados que los métodos estándar no pueden lograr. Los servicios integrados de perforación y doblado optimizan significativamente el proceso de producción. Según la investigación, la implementación de sistemas CNC para estos procesos reduce los tiempos de procesamiento en un 20%, ofreciendo un ciclo de producción más eficiente y fluido en acero inoxidable y otros materiales.
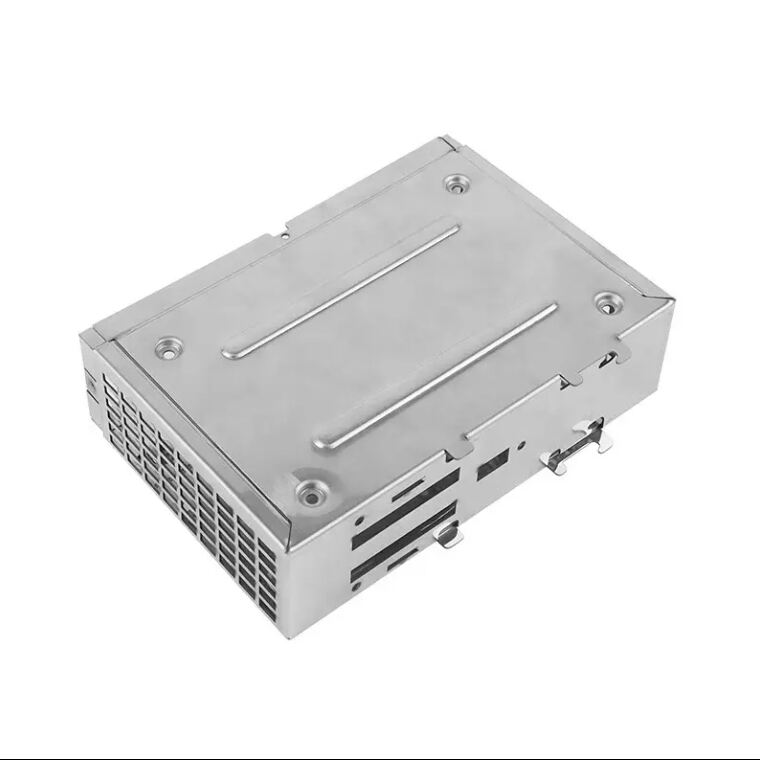
Tendencias Futuras en el Fresado CNC para Chapa Metálica
El Papel de la IA en el Aumento de la Eficiencia del Fresado CNC
La Inteligencia Artificial (IA) está desempeñando un papel fundamental en la transformación de la eficiencia de los procesos de mecanizado CNC. Al predecir las necesidades de mantenimiento, optimizar la configuración de las máquinas y analizar los datos operativos en tiempo real, la IA reduce significativamente el tiempo de inactividad y mejora la eficiencia operativa. Esta integración tecnológica no solo ayuda a mantener la longevidad de las máquinas, sino que también mejora la calidad y consistencia de la producción. Informes recientes indican que los fabricantes que emplean marcos de IA observan mejoras en la eficiencia operativa de hasta un 30%, gracias a capacidades de toma de decisiones impulsadas por datos más inteligentes. Este avance tecnológico subraya la dirección futura para los fabricantes que buscan mantenerse competitivos aprovechando la IA en el mecanizado CNC.
Tecnologías Emergentes en la Fabricación de Metales CNC
Innovaciones como la fabricación aditiva y el mecanizado híbrido están revolucionando la fabricación de metales CNC, expandiendo sus capacidades más allá de los métodos tradicionales. Estas tecnologías permiten la producción de geometrías complejas y apoyan un uso sostenible de los materiales. La integración de estas tecnologías emergentes en la fabricación permite una mayor flexibilidad, incluyendo la personalización y la prototipación rápida. Las proyecciones de la industria indican un aumento en la flexibilidad de producción superior al 25% en los próximos años debido a estos avances tecnológicos. Este crecimiento refleja el compromiso de la industria con la innovación, buscando satisfacer las demandas cambiantes de los clientes y los objetivos de sostenibilidad ambiental. A medida que el mecanizado CNC continúa evolucionando, los fabricantes están bien posicionados para beneficiarse de estos avances tecnológicos.
Torneado CNC: realizando la fabricación de piezas rotativas
ALLTecnología de tratamiento de superficies en mecanizado CNC: mejorando el valor añadido del producto
siguienteRecommended Products
Hot News
-
ventajas del mecanizado CNC
2024-01-16
-
¿Qué es la tecnología de mecanizado CNC?
2024-01-16
-
la tendencia de desarrollo del mecanizado CNC
2024-01-16