CNC lathe machining: realizing the manufacturing of rotating parts
CNC lathe machining is fundamental in crafting precise rotating components using advanced technology. This process, rooted deeply in computer numerical control (CNC) technology, automates the turning process, drastically enhancing machine precision and operator efficiency. Here's a deeper dive into its mechanics and benefits.
Core Mechanics of CNC Lathe Operations
CNC lathes leverage computer numerical control to automate the turning process, thereby enhancing machine precision and operator efficacy markedly. The process begins with feeding raw material into the lathe, where it rotates at high speed while cutting tools shape the material into specific geometries. Unlike manual lathes, CNC lathes can produce highly complex designs efficiently with reduced material waste. Operational data supports this efficient design production, evidencing up to 30% less waste compared to traditional methods.
Role of Computer Control in Achieving Tight Tolerances
The computer control systems in CNC lathes are crucial for ensuring manufacturing tolerances are kept within micrometer accuracy levels, which results in precise rotational symmetry. Such precision is vital in sensitive industries such as aerospace, where even minor deviations can have significant repercussions. Utilizing advanced computer algorithms allows CNC lathes to adapt continuously during the machining process, further improving accuracy by analyzing real-time feedback and adjusting operations accordingly.
Comparison with Traditional Metal Fabrication Methods
When compared to traditional metal fabrication methods, CNC lathe machining stands out by optimizing both speed and cost-efficiency in producing rotating components. Where traditional methods demand extensive manual labor and longer setup times, CNC machining effectively reduces production time by up to 50%. Moreover, an analysis of lifecycle costs indicates that CNC machining incurs lower long-term expenses due to diminished maintenance needs and material waste, thus proving itself as a superior alternative in various manufacturing scenarios involving rotating precision parts.
Key Advantages of CNC Lathe Machining in Rotating Component Production
Superior Accuracy for Complex Geometries
CNC lathes offer unparalleled accuracy in fabricating intricate designs with angular and radial features. These machines can achieve precision down to 0.01mm, a level of accuracy that is crucial for high-performance applications. This capability enables engineers to design parts that not only fit perfectly but also function optimally, which is especially important in sectors like aviation and automotive where precision is non-negotiable. Moreover, the use of statistical process control methods enhances this accuracy by continuously monitoring and adjusting machining parameters, ensuring each product meets stringent quality standards.
Enhanced Repeatability in High-Volume Manufacturing
One of the most significant advantages of CNC lathe machines is their exceptional repeatability, which ensures that every part in a production batch is consistently produced to the same specifications, thereby minimizing defects. This attribute is crucial in high-volume manufacturing, where consistent quality across thousands of units is required. Advanced programming and automation enable manufacturers to maintain high-quality standards while significantly improving output. According to industry statistics, companies utilizing CNC lathe technology can produce up to 90% more components in the same timeframe compared to traditional manual processes, showcasing its efficiency.
Integration with Metal Stamping and Forming Processes
CNC lathe machining seamlessly integrates with metal stamping and forming processes, allowing for enhanced production capabilities. This integration allows manufacturers to refine complex features without the need for retooling, thereby reducing lead times. The synergy between CNC lathe machining and these processes ensures a smooth workflow, enabling parts to move efficiently through production stages without unnecessary delays. This harmonious integration is vital for industries that demand quick turnaround times and precision, such as automotive and aerospace manufacturing.
Multi-Axis Machining Capabilities
Multi-axis CNC lathes represent a significant advancement in machining capabilities, allowing for simultaneous operations across multiple planes. This advanced technology facilitates the creation of highly complex parts in a single setup, removing the need for frequent repositioning or secondary operations. As a result, production times are significantly reduced, benefiting industries where precision and speed are critical, such as aerospace and automotive. By enabling the fabrication of more intricate designs, multi-axis machining reshapes traditional production paradigms, driving efficiency and innovation in manufacturing processes.
Live Tooling Systems for Combined Operations
Live tooling systems in CNC lathes offer a revolutionary way to streamline machining processes. By allowing drilling and milling operations to occur while the part is still rotating, these systems eliminate the need for stopping the machine to reload parts, thereby significantly reducing handling time. This innovation not only enhances efficiency but also expands the types of features that can be produced within a single machine setup. The versatility of live tooling is particularly advantageous when producing parts requiring various machining methods, making it a valuable asset for manufacturers seeking to optimize operations and reduce costs.
Real-Time Quality Control Through Automated Feedback
Automated feedback systems are integral to modern CNC lathes, ensuring real-time quality control during machining operations. These systems continuously monitor parameters to check the quality of parts, offering an immediate verification rather than the traditional post-production checks. Data gathered from these processes provides invaluable insights into potential areas for improvement, enhancing efficiency and product quality. Furthermore, the integration of IoT technologies amplifies these capabilities, allowing manufacturers to harness robust data for continuous refinement of their operations, ultimately paving the way for more effective and sustainable manufacturing practices.
Industry Applications of Precision Rotating Parts
Aerospace: Turbine Shafts and Engine Components
In the aerospace sector, CNC lathe machining plays a crucial role in manufacturing turbine shafts, requiring precise balance and aerodynamic properties. These components are vital for ensuring the reliability and efficiency of aircraft engines. Typically, parts produced for aerospace undergo rigorous testing and certification, given the high-stakes environments in which they function. With CNC technology, the industry has seen significant improvements in the production of lightweight and durable components, which enhance performance while maintaining safety standards. CNC machining has become indispensable in achieving the stringent requirements set by aerospace manufacturers.
Automotive: Transmission Parts and Drive Elements
CNC lathes are integral to the automotive industry for fabricating transmission parts and drive elements that demand consistent quality and reliability. These machines enable rapid responses to design changes and consumer demands without compromising quality. By facilitating the production of more complex parts, CNC technology has driven advancements in fuel efficiency and vehicle performance. The automotive sector has experienced a transformation due to CNC machining, streamlining processes and ensuring high-quality outcomes in a competitive market. This shift has been crucial for meeting the evolving standards of modern automotive manufacturing.
Medical: Implantable Devices and Surgical Tools
In medical applications, CNC lathe machining is used to create implantable devices and surgical tools demanding the highest levels of precision. Quality control is paramount in this field, with stringent regulations ensuring that only safe and effective products reach the market. The advancements in CNC technology have made customization of medical tools possible, enabling tailored solutions for specific patient needs. This innovation is pivotal in enhancing patient care, allowing for precise and reliable medical interventions. CNC machining thus stands at the forefront of modern medical device manufacturing, ensuring both innovation and adherence to rigorous health standards.
CNC Machining Solutions for Precision Rotating Components
Aluminum Parts with Precision Machining & Anodized Finish
CNC machining of aluminum parts is pivotal in creating components that are both lightweight and robust, serving a myriad of industries efficiently. Aluminum, when anodized, not only gains enhanced surface durability but also achieves superior corrosion resistance and appealing aesthetics. This makes such machined parts ideal for applications demanding both resilience and visual appeal. Additionally, the precision CNC machining ensures tight tolerances are maintained, which is crucial in scenarios where both weight and accuracy are critical. Discover more about the Aluminum Parts with Precision CNC Machining and Anodized Finish.
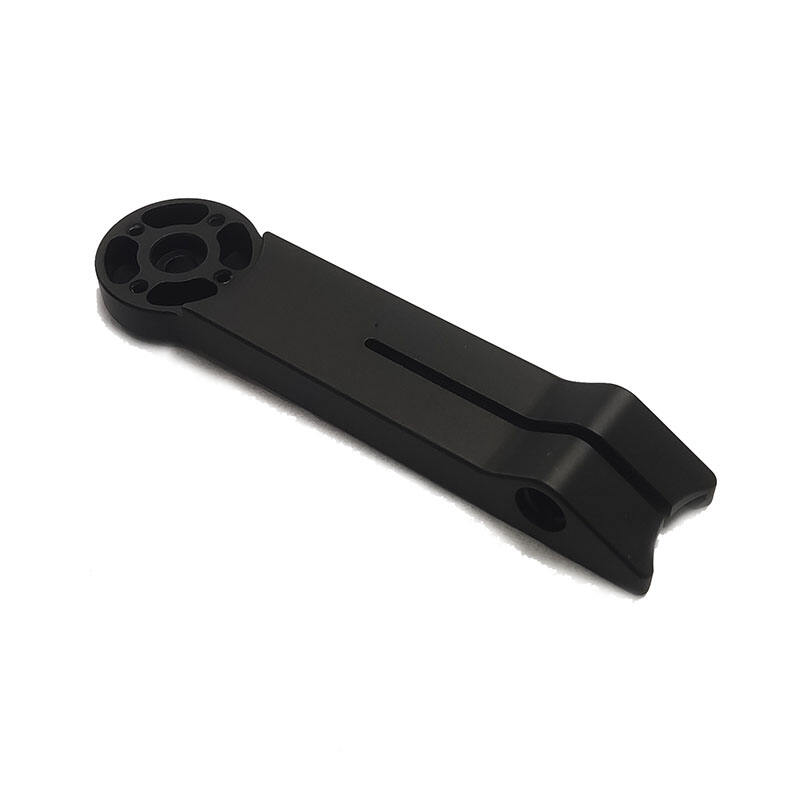
Custom Stainless Steel Milling for High-Stress Applications
Custom milling of stainless steel is indispensable for producing durable components used in high-stress environments like the automotive and aerospace sectors. The intrinsic chemical properties of stainless steel, enhanced by advanced CNC machining techniques, contribute to excellent corrosion resistance and unparalleled strength. This combination allows the creation of parts that can withstand extremities in stress without compromising on performance. Innovations in CNC drilling and milling further aid in improving processing speed, essential for meeting high-volume production needs swiftly. Explore the potential of OEM Custom Precision CNC Machining Stainless Steel milling Aluminum Parts.
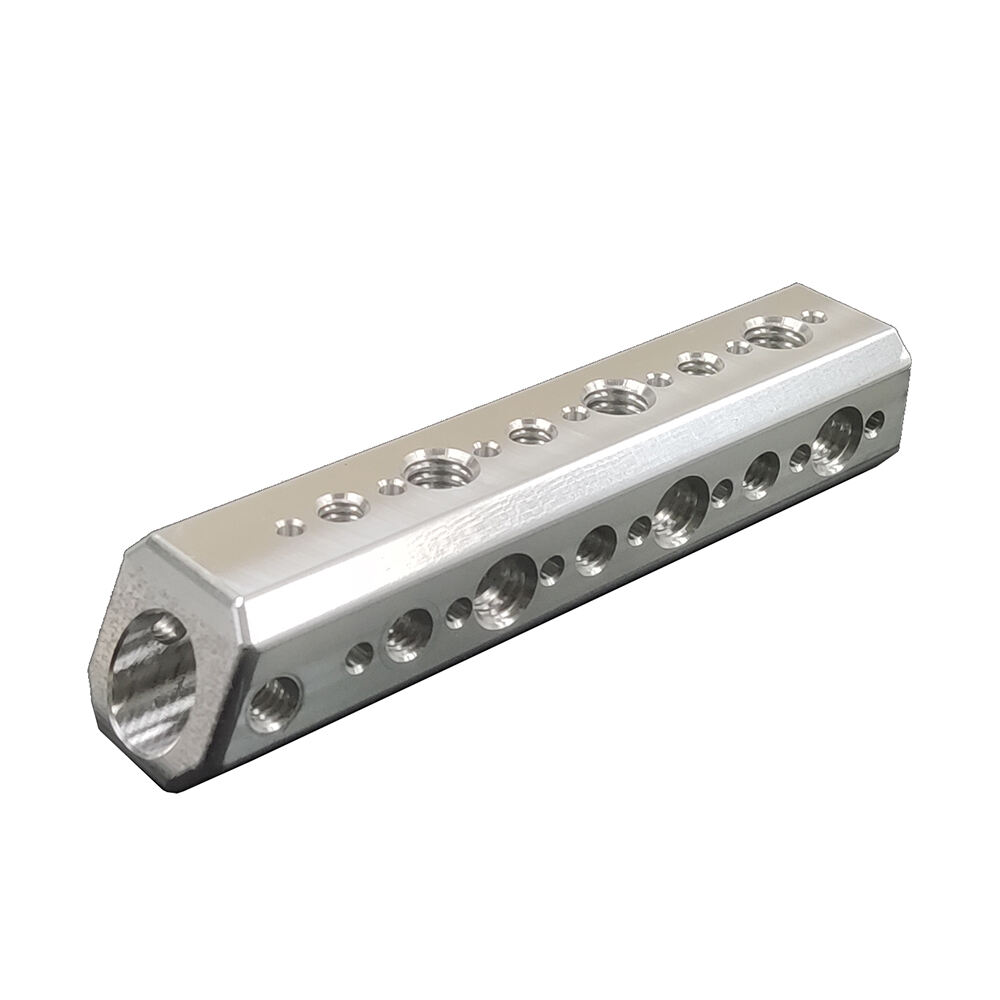
Rapid Prototyping Services for Complex Rotating Assemblies
Rapid prototyping services in CNC machining are transformative for manufacturers, providing the ability to swiftly develop and assess complex rotating assemblies before large-scale production. This service significantly shortens time-to-market, allowing companies to remain competitive while maintaining impeccable product quality through iterative testing. The continuous evolution in CNC technologies has further enhanced prototyping capabilities, allowing for faster and more intricate design iterations. This capability is particularly valuable in industries where speed and innovation are key differentiators. Learn more about Customized Precision Rapid Prototype Machining Service Stainless Steel Aluminum Parts CNC Metal Turning Cutting Milling.
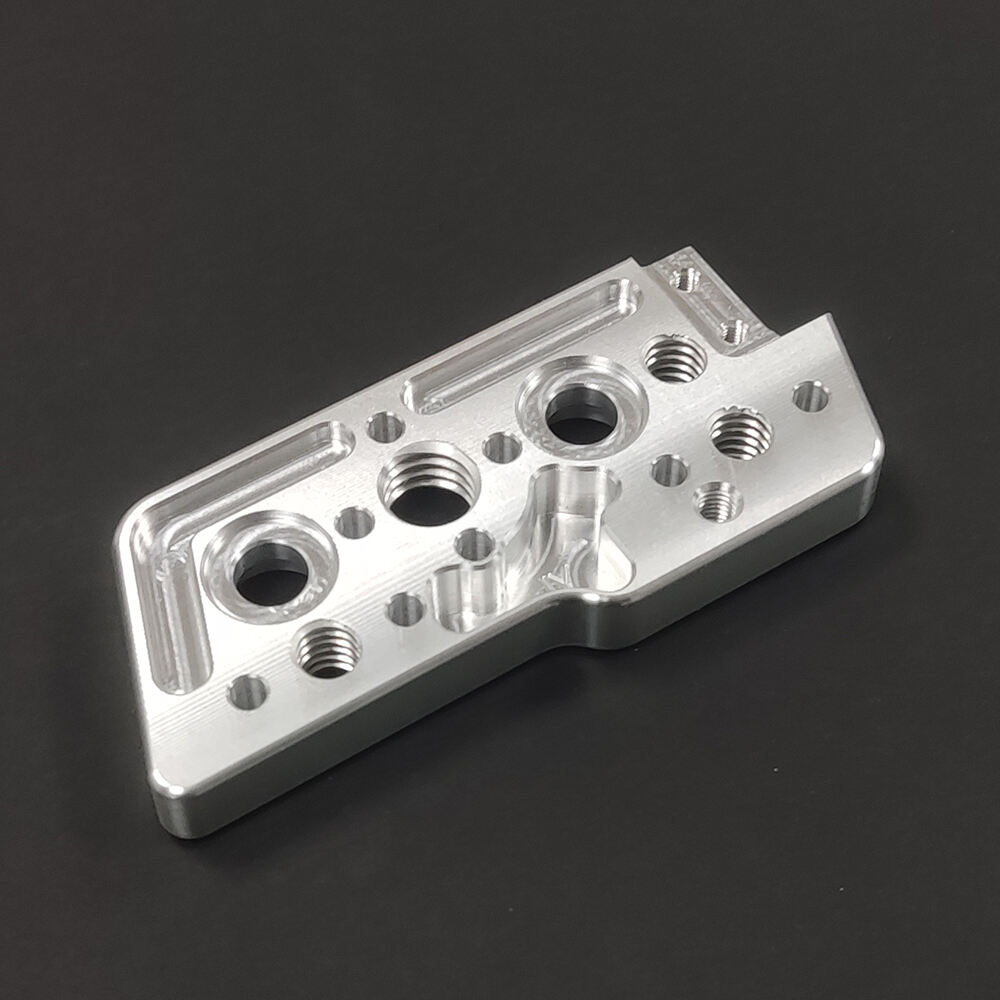
Selecting Optimal CNC Lathe Services
Material Considerations: From Sheet Metal to Exotic Alloys
Choosing CNC lathe services necessitates understanding the material type, whether it's sheet metal or exotic alloys, for successful machining. Different materials require specific machining strategies and tooling, which affects both production time and cost considerations. The properties of these materials, including strength, ductility, and corrosion resistance, must match application requirements to ensure end-product integrity and functionality. For example, sheet metal offers flexibility in design while exotic alloys can provide higher strength, essential for demanding environments like aerospace applications.
Evaluating CNC Router vs. Lathe Capabilities
Comparing CNC routers and lathes is crucial, depending on specific project needs. Lathes are particularly suited for machining rotational parts with high precision, while CNC routers excel in creating flat or three-dimensional designs. This comparative evaluation helps in selecting the most suitable technology for optimizing production processes and achieving efficient workflows. Understanding when to use each machine can ultimately lead to improvements in production efficiency and quality, ensuring that each project meets its unique specifications.
Certification Requirements for Mission-Critical Parts
For sectors such as aerospace and medical, knowing certification requirements for CNC lathe services ensures compliance and safety. Certified services undergo rigorous quality assurance processes to validate their capacity to deliver mission-critical components, which is crucial for regulatory adherence. Keeping up with the latest certifications is essential for manufacturers to stay competitive and maintain their quality assurance standards. Such certifications not only affirm the reliability of CNC services but also bolster trust with clients relying on excellence for vital parts.
Recommended Products
Hot News
-
Advantages of CNC machining
2024-01-16
-
What is CNC machining technology?
2024-01-16
-
The development trend of CNC machining
2024-01-16